“They don’t make ‘em like they used to.”
As tired as that adage is, it’s stood the test of time — like the structures, products, and engineering methodologies it describes. And in the case of one of the axiom’s longest-lived examples, recent Massachusetts Institute of Technology (MIT) research found stunning evidence for why.
Roman concrete is famously durable. The ubiquitously famous aqueducts have stood suspended in Italian valleys for thousands of years, as has the domed Parthenon and most of the Colosseum.
Why? Ancient artisans built it all out of a concrete mix that displays “self-healing” properties.
That’s right — MIT, Harvard University, and Italian and Swiss labs all think ancient Roman concrete has outlasted modern concrete by millennia because it can repair itself after hardening.
The findings appear in the journal Science Advances. For years, consensus held that the key to the ancient concrete’s durability was one ingredient: pozzolanic material, such as volcanic ash from the area of Pozzuoli, in the Bay of Naples. The Romans even shipped it throughout their vast empire as a construction component, and historians and architects at the time documented its importance.

A Roman aqueduct in Segovia, Spain. Photo: Shutterstock
But in its recent examinations, the MIT-led research team found an ingredient in the concrete that could be even more critical, hiding in plain sight.
Surprising properties
Tiny flecks of lime proliferate in the mixture. Previous researchers often discounted the small, distinctive, millimeter-scale minerals (known as lime clasts) as a byproduct of sloppy mixing techniques or carelessly-chosen raw materials. However, their presence provoked the MIT team’s curiosity.
“The idea that the presence of these lime clasts was simply attributed to low quality control always bothered me,” Admir Masic, the study’s main author, told MIT News. “If the Romans put so much effort into making an outstanding construction material, following all of the detailed recipes that had been optimized over the course of many centuries, why would they put so little effort into ensuring the production of a well-mixed final product? There has to be more to this story.”
There was. The group applied high-resolution multiscale imaging and chemical mapping techniques that Masic’s own lab team had developed. They discovered that the lime clasts came from a “hot mixing” technique that Roman concrete workers used with the precision of chemists.
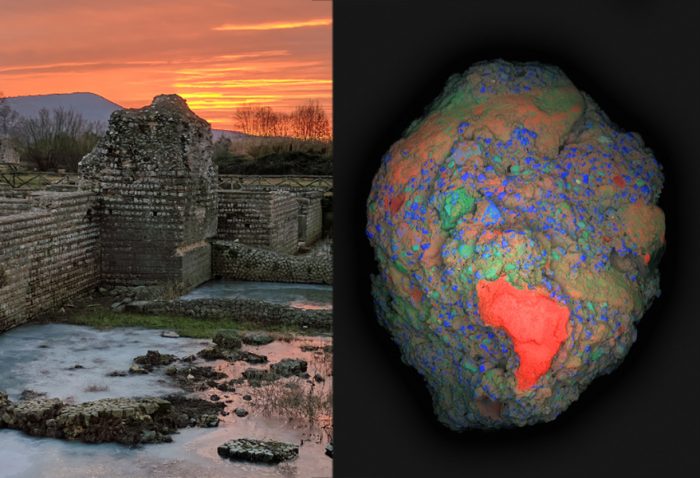
A 2 cm fragment of ancient Roman concrete (right) collected from the archaeological site of Privernum, Italy (left). The red blob on the sample is a lime clast. Photo: Masic et al
Spectroscopic examination provided clues that the clasts had formed at extreme temperatures, similar to the way modern quicklime is manufactured. The chemical compound develops a brittle structure during the hot mixing process. This leads to internal calcium deposits that fracture easily. That, the team proposed, could provide the hardened substance’s self-healing functionality.
As soon as tiny fractures start to form inside the concrete, they can “preferentially” make their way through the high-surface-area lime clasts, according to MIT News. The lime then reacts with water, which can recrystallize as calcium carbonate and quickly fill the crack — or react with nearby pozzolanic materials to strengthen the composite.
Tests inspire market push
Not satisfied to theorize based on looking at centuries-old concrete samples, the team made its own “Roman” concrete and stress-tested it.
The researchers produced and tested two sample lots of hot-mixed concrete: one with the lime clasts, and another with modern formulations. Then they deliberately cracked the hardened product and channeled water through the cracks.
Proof positive: Within two weeks, the cracks in the ancient formula had completely healed, fully preventing water ingress. An identical chunk of concrete made without the lime clasts never healed. The water just kept flowing through the sample.
Following the successful tests, the team is working to commercialize the modified cement material.
“It’s exciting to think about how these more durable concrete formulations could expand not only the service life of these materials but also how it could improve the durability of 3D-printed concrete formulations,” Masic said.
Maybe, one of these days, they will start making them like they used to.